Stainless Steel Passivation
Stainless Steel Finishing
The Best Defense against corrosion
Stainless steel passivation is used to locally remove the iron component of the stainless steel at the very surface of the part. This in effect leaves the surface more resistant to corrosion marks and staining, ensuring that the parts will look good longer than if not passivated.
Wisconsin Finishes uses Citric acid passivation which is a more environmentally-friendly method than the traditional nitric acid process.
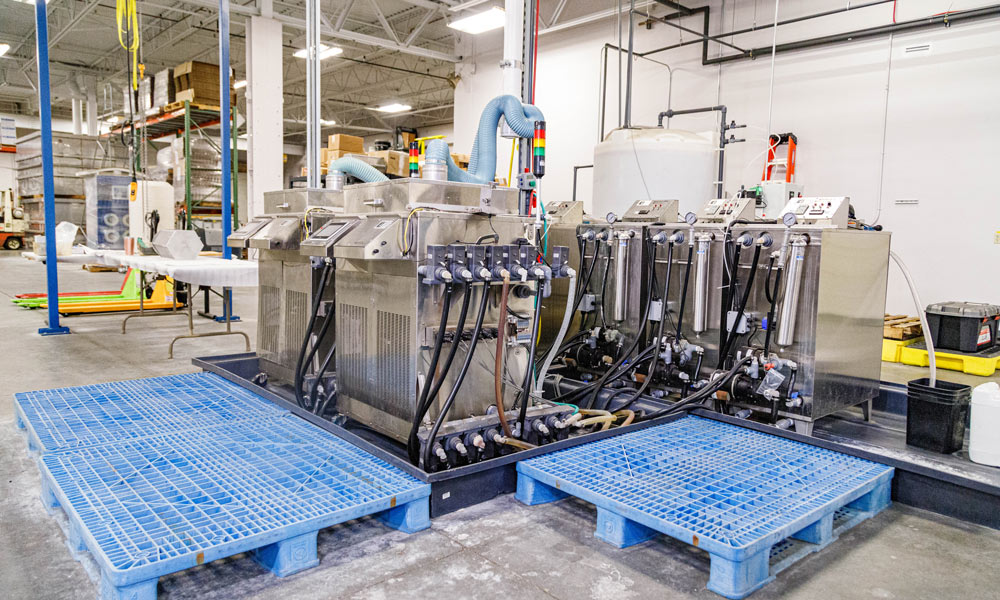
Offering Selection
Process | Clear Anodizing | Black Anodizing | Chemfilm | SS Passivation |
---|---|---|---|---|
Material used on | Aluminum | Aluminum | Aluminum | Stainless Steel |
Coating thickness | 0.2 – 0.8 mil | 0.6 – 1.2 mil | 0 – not measurable | 0 – no coating buildup |
Dimensional increase | ~50% of coating thickness | ~50% of coating thickness | None | None |
Electrical conductivity | None, insulator | None, insulator | Type 3 – very good; Type 1A – good | No change from base material |
Specifications | MIL-A-8625F type II class 1 | MIL-A-8625F type II class 2 (black) | MIL-DTL-5541 type II, class 1A and 3 | AMS2700 method 2, ASTM-A967 citric 2 |
Appearance/color | Gloss silver to matte silver | Medium gloss black to matte black | Slight yellow to blue tint to base material. Some light streaking possible | No change to base material – SS appearance |
Corrosion resistance | Very good – 336 hour salt spray | Very good – 336 hour salt spray | Good – 100 hour salt spray | Excellent – no salt spray corrosion |
ELV/WEE compliant | Yes | Yes | Yes | Yes |
Cost of process | $$ | $$$ | $ | $ |
Max part size at WFL | 30″ x 30″ x 48″ | 30″ x 30″ x 48″ | 30″ x 40″ x 108″ | < 5" - bulk barrel |